If we go back to the early electronic fuel injection, (EFI) systems known as batch-fired injectors or what was called simultaneous EFI systems, for example, from a V-6 engine, the bank 1 injectors were all fired together. The next engine revolution resulted in the powertrain control module (PCM) group firing the injectors from bank 2.
These engines usually had a single upstream O2 sensor to sample the O2 molecules or the lack thereof from both banks. On these early systems, when an injector electrically lost its resistance value or had a problem called pintle distortion, it created a rich condition on that specific cylinder and bank. The result is that the one upstream O2 sensor voltage was latched high indicating a rich condition. See Fig 1.
This problem caused the PCM to lean out all six injectors at times, and that created a lean density misfire on the other five good cylinders. The resulting symptom was a rough choppy idle condition that stressed the catalytic converter’s emission control capability. Then the manufacturers went to sequential injectors in the mid-80s on some engines. These systems usually had separate O2 sensors for bank 1 and bank 2. On these systems, if one injector created a rich condition, the PCM would recognize a rich condition from just that one bank. The result was that the PCM would lean out all the injectors on that bank and still could create a lean density misfire from the other cylinders on that bank. The opposite also could occur, whereas an individual injector that is severely restricted could cause an O2 low voltage and a lean condition.
The PCM would then increase the injector on-times for all the injectors on that bank. The result could easily create a rich density condition on the other cylinders and poor fuel economy. The symptom, in both cases, was usually a rough choppy idle condition that stressed the catalytic converter. It reminds us of the importance of comparing the total fuel trim values of both banks.
For example, if the total fuel trim values are plus 15% in bank 1 and the total fuel trim values on bank 2 are minus 3%, we know that there is an air-fuel ratio problem on bank 1.
Good comparisons of total fuel trim values from bank to bank should always be between plus or minus 10% under all load conditions while being in a closed loop. A pressure drop test, which is conducted during Key on Engine Off (KOEO) using a scan tool to command each injector to pulse while looking for uniform fuel pressure drops using a fuel pressure gauge, was taught by one original equipment manufacturer (OEM). On those systems, I have personally done this test dozens of times and have come up with inconclusive results.
Some aftermarket testers are available to monitor the fuel pressure drops while tying in a pressure transducer in the fuel pressure line and looking at the uniformity of the fuel pressure drops when an injector is pulsed and using a pressure transducer coupled to a digital storage oscilloscope (DSO). The challenge here is how to tie in the pressure transducer into the fuel pressure line on various makes and models. Another aftermarket company is using a pressure transducer hooked into the vacuum control port of the fuel pressure regulator and viewing electronically with a DSO the pulses in the rail as each injector is pulsed.
What I had done (and taught) way back in the ‘90s on the sequentially injected engines was to monitor the O2 sensor when we commanded an injector off during Key On Engine Running (KOER) conditions with a scan tool. If the injector was commanded off and totally shut off the fuel to that cylinder, we have effectively turned that cylinder into an air pump and the O2 sensor should make a major lean shift with the O2 voltage going low. While this was a good test to find leaking injectors that caused a rich condition, it didn’t help much in finding injectors that suffered from olefin buildup in the injector pintle area that caused lean cylinder misfire conditions.
Fig. 2 shows this test from a Chrysler 3.8L engine. Notice before an injector was commanded off, the O2 voltage reads 3.1 volts. Beginning in model year 1997, the Chrysler systems used a five-volt bias voltage to their zirconium style O2 sensors. With the loading effect with the O2 sensor connected, the bias voltage during KOEO was pulled down to 2.5 volts. With the engine running and in a closed-loop, voltages above 2.5 volts represent a rich condition while voltages below 2.5 volts represent a lean condition. While using a scan tool to conduct this test, the PCM maintains an open-loop strategy. This particular engine was running rich with a rich code. Notice in Fig. 3 that as we commanded an injector off the O2 voltages went to 2.5 volts on all cylinders. This pretty much tells us that an injector was not leaking fuel, causing this rich condition. We observed major fuel pressure fluctuations during our diagnosis. We concluded that the fuel pressure pulsator in the rail had to be defective.
After removing the C clip, we found a broken spring. The fuel pressure pulsator is designed to absorb the pressure surges in the rail as the injectors pulse.
In the evolution of electronic fuel injection (EFI) engines, most manufacturers have gone to the sequential EFI systems. The V-6 and the V-8 engines have a separate upstream O2 sensor for each bank. The four-cylinder engines still use a single upstream O2 sensor.
Beginning in model year 2011, some manufacturers had introduced individual cylinder fuel control strategies known as individual cylinder fuel control (ICFC). Take a look at Fig. 4. Notice that in model year 2011, 25% of the vehicles are equipped with ICFC. In model year 2012, 50% of the vehicles are now equipped with ICFC. In model year 2013, 75% of vehicles have ICFC.
Government mandates in model year 2014 required all manufacturers to equip their engines with ICFC strategies. Normally, you would think that the manufacturers would have each exhaust port with its own individual O2 sensor, but that is not how the systems are built. We still use a single upstream O2 sensor on the four-cylinder engines and a single upstream sensor for each bank on the V-6 and the V-8 engines.
Before we go into detail on the ICFC systems, let’s look at a good uniform O2 sensor pattern by using a DSO in Fig. 5 with the focus on a good O2 sensor and good short-term fuel trim values. Now notice Fig. 6. This was captured from a lean density misfire. Notice that the short-term fuel trim numbers increased and the O2 responded by going momentarily rich. If this problem were consistent, the long-term fuel trim values would also increase. With this new technology from the individual cylinder fuel control equipped engines, we cannot ignore the reliable parameters of short-term and long-term fuel trim values. The zirconium O2 sensors shift from a lean condition to a rich condition and back to lean at between 2 and 5 HZ. The issue we had with the zirconium O2 sensors is that they can only see a rich air-fuel at a 14-to-1 ratio. The zirconium O2 sensors cannot see a lean shift past a 15-to-1 air-fuel ratio. The new type of O2 sensors are known as a wideband O2 sensor, and they can see an air-fuel ratio of the rich side all the way to a 1- to-1 air-fuel ratio. They can see all the way to an 18.5-to-1 lean condition. See Fig. 7.
On some modern-day engines equipped with an electronic fuel control module and an electronic fuel pressure sensor, we have the ability to monitor fuel pressure drops during KOER conditions as we monitor the fuel pressure drops as we disable one injector at a time using a scan tool. This 2012 Chevy Equinox with a 3.0L engine equipped with gasoline direct injection (GDI) exhibited a rough running misfire symptom on a cold startup. In the Mode 6 menu, two cylinders showed single-digit misfires from the most recent 10 drive cycles. We conducted the injector balance test after a cold soak condition. Notice the results in Fig. 8. Notice the two injectors that indicated a 68 PSI drop. There are times in our business when we have to make a judgment call. We communicated to the vehicle owner that we would recommend an intake and injector cleaning as a first step. Notice the results after that service was completed in Fig. 9.
In my opinion, this is going to be an important test to locate faulty injectors that cause the common code P219A found on engines equipped with ICFC. Keep in mind that this code does not isolate a specific cylinder. Mode 6 data for misfires from each individual cylinder from the last 10 drive cycles should help in finding the cylinder that may have caused the P219A individual cylinder fuel control code. Also, on GM systems, don’t forget about the history misfire counters found on the enhanced side of the scan tool.
This seems to be the age of virtual learning, so we are going to apply that term to the ICFC systems. The PCM is programmed to learn top dead center (TDC) from the crankshaft position sensor (CKP) and camshaft position sensor (CMP) sensors for TDC of cylinder No. 1 as well as the firing order. The injectors on these engines are all of the sequential type. On the port fuel injection (PFI) sequential systems, the injectors were pulsed at the end of the exhaust stroke right before the beginning of the intake stroke. At 180 degrees later, we had the intake stroke. And 180 degrees after that, the compression stroke occurred. A few degrees before the TDC of the compression stroke a firing event occurred beginning the power stroke exhaust. And 180 degrees later, the exhaust stroke occurred. ICFC equipped engines cannot determine which cylinder emitted the exhaust stroke, but rather, there is a fuel imbalance problem. Let’s look at Fig. 10. If this O2 sensor indicated a consistent rich shift as indicated here, the strategy would be met to set a P219A code. Remember that the zirconium O2 sensor will shift from lean to rich and back to lean at 2 to 5 HZ. As the engine RPM increases, you can imagine that the frequency of the exhaust pulses are much higher than 2 to 5 HZ. That would pretty much tell us that we have some limitations on this code.
The reality here is that mechanical issues such as leaking valves or compression loss will also affect the combustion process. To sum this up, I can tell you the individual cylinder misfire monitors should be paramount in our diagnostics in reference to the P219A ICFC codes. Engines equipped with ICFC strategies do not have the ability to flag the specific injector or cylinder that is causing a lean or rich condition, nor does the PCM have the ability to adjust the injector-on time from a specific injector or cylinder that is running too rich or too lean. That is why the misfire data in Mode 6 from the last 10 drive cycles or the history misfire counters are paramount to investigate.
Let’s take a look at the code criteria for the P219A code in Fig. 11. Notice that it says that multiple samples of the upstream O2 sensor accumulated voltages are consistently greater than the desired value. I am now reading between the lines and considering if a cylinder went lean from say a restricted injector, the PCM would recognize that and the fuel trim values would increase thus increasing the injector-on times of all injectors and this would create the O2 voltages to be greater than the desired value. What I am saying here is that a lean cylinder that creates a low O2 voltage can be flagged as well as a cylinder that is running rich, creating greater than desired O2 voltages. The important thing to remember here is that ICFC strategies cannot detect a specific cylinder with a fuel control issue, nor can it adjust the injector-on time for an individual cylinder.
A problem vehicle once came in with a malfunction indicator lamp (MIL) and a code P219A. The car owner did not experience any symptoms. The MIL light would not go out. The previous dealership had replaced the coils, the spark plugs and the injectors but to no avail. The vehicle is a 2015 Chevy Malibu with 67,000 miles on the clock. This is a GDI vehicle with a 2.5L LKW engine. First, let’s take a look at the freeze frame data in Fig. 12.
Notice the 70% engine load at 3,200 RPM. The vehicle was in closed-loop with the short-term fuel trim indicating minus 6% while the long-term fuel trim numbers indicated plus 4%. This represents a total fuel trim value of minus 2%, which is nearly ideal. The confusion that begins here is that the PCM sets an ICFC code and our total fuel trim values are nearly perfect. While we are investigating the freeze frame data, let’s look at the low-side and high-side fuel pressure values that were captured in Fig. 13.
Notice the good low-side and high-side fuel pressure values. Using the scan tool set up in the record mode, a test drive was conducted. See Fig. 14. Notice the No. 3 cylinder live misfire counters.
Using a smoke machine, we applied smoke machine pressure to the No. 3 cylinder. After rotating the engine several times, we finally discovered smoke waffling up from the intake. Since this is a GDI vehicle and carbon buildup is common on the intake valves, we recommended trying a chemical cleaning of the intake. It’s another case where we had to make a judgment call and communicated this to the car owner. Could it be a loss of compression? Of course. However, we are familiar with this problem on GDI engines and are aware of the fact that intake cleaning on these systems should be a periodic maintenance procedure. In closing, what I have tried to convey to my fellow technicians is that in the event of a P219A code, investigate the misfire monitor data to try to isolate the problem to a specific cylinder. Mechanical issues will always have an effect on a cylinder’s combustion process and will affect the exhaust gasses.
The industry is better because of your commitment.
Bill Fulton is the author of Mitchell 1’s Advanced Engine Performance Diagnostics and Advanced Engine Diagnostics manuals. He is also the author of several lab scope and drivability manuals such as Ford, Toyota, GM and Chrysler OBD-I and OBD-II systems, fuel system testing, and many other training manuals in addition to his own 101 Lab Scope Testing Tips. He is a certified Master Technician with more than 30 years of training and R&D experience. He was rated in the top three nationally on Motor Service magazine’s Top Technical Trainer Award and has instructed for Mitchell 1, Precision Tune, OTC, O’Reilly Auto Parts, BWD, JD Byrider, Snap-on Vetronix and Standard Ignition programs. You may have also seen Fulton in many Lightning Bolt Training videos and DVDs and read his articles in many auto service magazines. He owns and operates Ohio Automotive Technology, which is an automotive repair and research development center and where the images for this article were produced.
About the Author
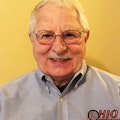