MOTOSHOP contest winner: The values of old meet the technology of tomorrow
RALEIGH, NC — Brown’s Alignment has thrived for nearly 30 years by maintaining its core value of giving customers quality service at a fair price. What the shop lacks is the technology to stay competitive in today’s market.
Based in Raleigh, NC, Brown’s Alignment was selected from nearly 1,000 entries as the grand prize winner of the 2015 MOTOSHOP Technology Tools $10,000 Shop Technology Makeover.
“Our panel of judges was humbled by the hundreds of dedicated, deserving shops across the country that entered the contest, said Jad Dunning, vice president and general manager of MOTOSHOP Technology Tools. “We’re confident the technology makeover awarded to Brown’s Alignment will help their shop continue to deliver a great quality of service to its customers, and do so in ways that are new, exciting and efficient.”
A Black & Decker engineer for more than nearly 30 years, Bayne wanted to remain in his Raleigh neighborhood with his wife and three children when the company was looking to relocate in the mid-1980s. Rather than uproot the family, he and Ann purchased the shop.
“At the time, Buster Brown was a very popular line of shoes, so we decided to keep the name because it was easy for people to remember,” Ann told the MOTOSHOP Technology Tools team, which surprised Brown's with the contest win announcement during an in-shop visit in early October.
After about 10 years, son Scott joined the business, followed five years later by son Bryan. The eight-bay shop also has three technicians and an office manager.
The shop also does not monitor daily or weekly car count or average repair ticket amounts. Brown’s currently keeps all paper repair orders and invoices — organized by bookkeeper Ann — which makes searching customer history tedious and time consuming.
“We want to get into more maintenance, but we are reluctant to push our customers. But if we approach them properly, I think this will be a great success,” Bayne said.
“The MOTOSHOP Suite is about improving operations in the shop from helping to attract and retain customers to turning bays, automating functions. We expect to see Brown’s make progress in all these areas, as our tools help improve their operations day to day,” said Dunning. “But it is always a challenge to do something new, and it takes time to get comfortable. We recognize that adapting to new technology can seem overwhelming, and our goal is to remove that burden. We build products to be as easy to use as possible, and they will have a support staff always at hand.”
This support team includes a dedicated representative who will provide ongoing training and assistance to Brown’s, along with the MOTOSHOP hotline, which can address questions and software issues.
Bryan said he looks forward to having a partner to help this forward progress. “MOTOSHOP continues to grow, and we hope to keep growing along with them,” he said.
And he also has the support and encouragement of the shop staff. “Our technicians all came from dealerships, and they have seen the technology capabilities. They really deserve the credit for pushing us to move forward with this,” Bryan says.
And Office Manager Eric Baxter agrees that the potential improvements technology could bring to their business almost seem surreal. “Having customer history at our fingertips would be dreamy,” Baxter said.
“I don’t know that we are the cheapest, but we try to use quality parts, we want repairs to last and customers to feel good. We try to educate our customers and always give them good service,” Bryan said.
MOTOSHOP Technology Tools will again host the contest in 2016. Look for further details of how to enter coming the spring of 2016.
About the Author
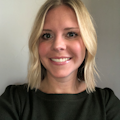
Krista McNamara
Krista McNamara is the former Editorial Director for the Vehicle Repair Group at Endeavor Business Media. She oversaw five brands — Motor Age, PTEN, Professional Distributor, ABRN and Aftermarket Business World. She worked in the automotive aftermarket industry for more than 15 years.