In our previous Part One article on the Anatomy of a Waveform, we talked in detail about the diagnostic value of scope checking the secondary firing events in reference to detecting lean conditions, rich conditions, low compression issues, open or shorted secondary circuits and weak coils by using a DSO. In Part Two, we are going to cover the diagnostic value of scope-checking the primary side of the ignition system on a voltage trace and by using a low inductive amp probe to monitor coil charge values and analyze ignition events.
On some modern-day engines, access to the secondary side of the ignition system is not easy and on some engines not even possible. In reference to the Ford and Chrysler systems, the PCM controls the primary side of the coils, so accessing the primary ignition waveform will give us the same info as to what we covered in the Anatomy of a Waveform when we covered the secondary ignition waveforms. On other COP-equipped engines where the igniter is integrated into the coil, it is not possible to obtain a primary voltage waveform. However, later on, we will cover the diagnostic value of using a low inductive amp probe to check and analyze a coil’s primary charge events.
In reference to primary voltage waveforms, let’s take a look at Figure 1. Point A is the dynamic voltage from the negative terminal of the coil. Notice the voltage per division on the scope is set at 10 volts per division. Above the ground tick mark, we see a good 12 volts. Point B is the point of primary turn on and the coil charge process begins. Point C verifies good ground integrity of the ignition module of primary drivers. Point D is known as a current limiting hump and is not found on all systems. At 10 volts per division, we don’t see the full amplitude. These primary firing line voltages will typically vary between 250 volts to 350 volts depending on the system.
The most important point is point E which is the sparkline or spark duration period. At a 2 milli-second scope time base, you can see a good 1.8-millisecond spark duration period. The important point here is that the spark duration period on a primary waveform will mirror that of a secondary waveform. Let’s take a look at a dual-trace example in Figure 2.
Channel 1 indicates the primary side of the coil, and channel 2 indicates the secondary side of the coil. Note that the sparkline angle and spark duration periods are identical to each other. This was captured during park-idle-no load conditions. Notice the short spark duration periods on both waveforms at 1ms per division. In addition, notice the upward angle of the sparkline due to lean conditions. If this were captured during a light load power brake condition you would see the upward angle more pronounced and the spark duration period shorten up with an increase of turbulence on the sparkline. This is an example of a lean cylinder where the nonconductive air molecules cause a short spark duration period. Figure 3 primary waveform indicates a very short sparkline. Look closely at the split firing line indicating an open in the secondary circuit. In Figure 4 captured from a performance engine with HEI ignition, note the long spark duration period of more than 2 milliseconds. This is a performance engine tuned into a rich 11-to-1 air-fuel ratio. This is another example where the conductive properties of fuel molecules will extend the spark duration period and the lack of conductive fuel molecules as in a lean condition will shorten the spark duration periods. If this were a passenger car engine in closed-loop maintaining an air-fuel ratio of 14.7 to 1, the spark duration period would be very close to 1.5 milliseconds.
In addition, if we drop the voltage per division down to 10 volts per division we would magnify the sparkline characteristics further. For those of you that have the Snap-on scopes, the voltage setting on the screen represents the total screen voltage, instead of voltage per division. The same applies to the time scale. If you want to set the time base to a 1ms per division you would set the time base icon (sweep speed) to 10 ms per screen on the horizontal screen. 10 divisions at 1 ms per division equal 10ms. Most other DSOs voltage and time icons represent the time and voltage per major division.
In reference to the Ford and Chrysler systems, the primary drivers are inside the PCM, so it is easy to back probe the negative terminal of a COP coil to obtain a primary waveform. If the coils are not accessible, we simply reference a schematic and probe into the specific primary circuit for a specific cylinder. A critical point here is that using a DSO and back probing the negative terminal of the coil the scope is hard-wired into the circuit, unlike secondary where we are inductively picking up a magnetic field. A primary ignition voltage waveform will be more stable compared to a secondary one. We talked about the heavier potted coils on modern-day COP systems in our Part One article on the Anatomy of a Waveform where the magnetic field was too weak to obtain a stable secondary firing event even when using a COP wand. We stated the need to use a secondary lead between the COP unit and the spark plug with a secondary KV probe around the lead in order to obtain a good secondary waveform.
We are aware of modern-day systems where the coils are buried under the intake plenum and access to the secondary or primary side of the coil is not possible. The systems by many manufacturers such as GM, Honda and Toyota COP units have the igniter integrated into the coil. The PCM forward biases the igniter to turn on current flow and begin the coil charge process. With that in mind, let’s bring in the low inductive amp probe (see Figure 5), and with a wiring schematic, we can clamp the amp probe around the primary positive feed wire or the negative wire of the coils. In some cases, as in Ford and other systems, we may have a dedicated fuse that supplies B+ to the coils. We can simply current ramp the coils by using a jumper lead across the female terminals of the ignition fuse. The arrow on the amp probe is faced in the direction of the current flow.
Pay attention to the attenuation values of the three different probes in Figure 5.
The probe on the left and the center probe, when set on the 100mv = 1 amp, means when the scope is set to a 100mv per division on the vertical scale then every division on the vertical scale equals 1 amp. For example, when current ramping a primary event, if the trace is 5 divisions above the ground tick mark it represents a 5 amp event. The other setting on the amp probe on the left is that for every 10mv setting per division on the vertical scale of the DSO equals 1 amp. The amp probe in the middle has a single setting in that for every 100mv setting each vertical division equals 1 amp. This is a popular setting when current ramping a primary coil event. The amp probe on the right has two settings. First, the 1mv setting per division on the DSO vertical scale equals 10ma. As an example, if the trace is 3 divisions above the ground tick mark, you are seeing 30ma. The other setting means for every 1mv setting equals 100ma.
With this setting, if the trace is 3 major divisions above the ground tick mark, you are seeing 300ma.
First, let’s look at the anatomy of a primary ignition amperage waveform in Figure 6. Note the point of primary turn on. We have dropped the voltage per division from 100mv equals 1 amp down to 50mv per division to magnify the point of primary turn on and get a good view. Do you see those small oscillations?
If they are not there, it means there is a problem. We will cover these oscillations in detail later. Note, the uniform gradual slope of the ramp. The modern-day primary and secondary ignition systems are divorced, meaning there is no connectivity between the primary coil windings and the secondary coil windings. As the primary magnetic field begins to build on the primary side of the coil, an opposite polarity secondary magnetic field begins to build on the secondary side of the ignition system. These two magnetic fields are of opposite polarity. The opposite polarity creates a counter voltage effect that creates the oscillations at the point of the primary turn-on. Now take a look at a magnified dual-trace example of the point of primary turn on from a secondary voltage waveform versus the point of primary turn from a primary amperage waveform in Figure 7.
You may be thinking as to how this could fit into your diagnostic strategy. Think about all of those engines where the coils are buried under the intake plenum or under the valve cover. Think about a no-start condition where you need to check for spark. In addition, what about a PO300 code?
Let’s take a look at the good, the bad and the ugly. First, in Figure 8 note the uniformity in all three coil charge events. At 100mv equals 1 amp, the amplitude indicates good coil saturation values. In Figure 9 from a 4 cylinder engine with the coils hidden under the valve cover, note the first amperage event. The initial oscillations at the point of primary turn-on are missing. In addition, note the steep current ramp. The problem was a totally fouled spark plug. A dead short to ground or shorted secondary windings could also cause this. Note that the second current event has the initial oscillations and a normal slope and normal saturation values. Now let’s look at another problem in Figure 10. Notice the uneven transfer of energy at the point of primary turn-off indicated by the amount of hash. The problem was caused by internal coil carbon tracking. Another example involves the diagnostic value of the amp probe in a 2007 Honda Odyssey with a dead miss and no MIL or codes. I could feel a dead miss as I pulled the vehicle into the stall. We clamped around the voltage feed wire to the COP units and found a missing current event. Let’s take a look at Figure 11. The PCM forward biases the igniters which are integrated into the COP units. A rising edge to 5 volts turns on the primary current flow and charges the coil. When the PCM shifts the 5 volts to 0 volts the primary magnetic field collapses and is mutually inducted into the secondary windings and the coil fires. With a wiring schematic, we identified the voltage primary feed wire to the coils as well as each coil’s individual PCM igniter control wire. A dual-trace example can be seen in Figure 11. The number 3 IGT trigger signal can be seen on channel 1 with a missing coil charge event for the number 3 coil.
If you have been down this road before it would not surprise you that the number 3 coil is buried under the plenum on the backside, so access to the coil was not possible. This is another example where the amp probe proves to be valuable. After replacing the number 3 coil and, of course, the spark plugs, let’s look at Figure 12. Look very closely at the current ramp value of the number 3 new coil. Does it match the other OE coils values? It looks to be about a half of an amp short compared to the OE coils. The misfire is now gone and out the door the car goes.
Most modern-day systems will disable the injectors when a type A or type B misfire occurs to save the catalytic converter. Most systems run the misfire monitor by noting the crank sensor’s numerator values. When a misfire occurs, the crank speed slows and the time value between the crank speed sensor toggles increases. In addition, the PCM will force the engine back into an open loop. When a misfire occurs while in closed-loop, before the PCM forces the engine into open loop, positive fuel trim values point to a lean density misfire while negative fuel trim values point to an ignition failure or a rich density misfire. It is important to capture fuel trim values while in a closed-loop when a misfire occurs.
Some Asian systems such as Toyota, Lexus, Scion, Kia and Hyundai use a different strategy. The Toyota, Lexus and Scion systems use two terms, one signal being IGT, meaning the igniter trigger signal. This is the digital signal from the PCM to control the igniter which is integrated into the COP unit. The rising edge of the IGT signal turns primary on while the falling edge turns primary current flow off causing the magnetic field to collapse and the coil fires. The other acronym is known as IGF, meaning ignition confirmation. I like to call this a signal ignition failure signal. This signal is used by the PCM to confirm that a coil charge event has occurred. The IGF circuit is integrated into the COP unit. When the coil is properly charged, the IGF voltage is pulled low. If the PCM does not see the IGF signal pulled low, it will disable an injector. A shorted COP unit can kill the IGF signals to the PCM resulting in a no start with a loss of injector pulses.
First, let’s look at a Toyota ignition schematic in Figure 12A. To current ramp the coils, we would simply install a jumper lead across the ignition fuse. Let’s take a look at a Toyota no-start problem in Figure 13. Using an amp probe, notice that the green trace indicates that all four of the coils were charged. The red trace represents the IGF signal. When the PCM thinks the coils are properly charged the IGF signal is pulled low individually per coil and then the voltage is released back to five volts. Notice that the IGF signal is staying low. This will cause the PCM to shut off the injectors resulting in a no start.
Now let’s take a look at Figure 14. The number one coil has been disconnected. We are now triggering off the No. 2 IGT circuit. Notice that the IGF signal returns to normal and the engine starts and runs albeit on three cylinders.
The Hyundai and Kia systems use a similar but somewhat different strategy to confirm primary firing events. First, let’s look at the ignition components in Figure 15. Focus first on the Ignition Failure Sensor. Looking at a schematic in Figure 16, notice that battery plus voltage comes into terminal number 4 and then goes through a current limiting resistor inside the Ignition Failure sensor and then exits terminal 3 to supply voltage to the coils. This resistor is known to burn out which causes a no-start/no-spark condition. A simple ohmmeter check can confirm an open. On a good system, when a coil fires, the Ignition Failure Sensor will send a 12-volt pulse to the PCM on the IFS circuit. In the event of a loss of the IFS signal to let’s say number 3 coil, this will cause the PCM to shut off the number 3 injector. Take a look at an ignition waveform from a Hyundai 3.5L engine in Figure 17
When a coil fires, the Ignition Failure Sensor will send a 12-volt pulse to the PCM. A failed coil or a failed igniter drive circuit will cause the PCM to disable an injector. Notice that the 12 volts IFS signal lines up perfectly with the point of primary turn-off of the amperage waveform. When you are current ramping these systems look for a dedicated ignition fuse. Figure 18 shows an ignition schematic. Removing the ignition fuse and using a jumper lead, we can current ramp check for proper coil saturation values.
Do you remember the last time you had a no-start on a PFI vehicle? You checked for good spark and good fuel pressure and decided to grab your noid light or test light to check for injector pulses? In reference to GDI injectors, the rules have changed. Noid lights or test lights will not work. An amp probe signal trace would be needed or a dual-trace voltage waveform would be needed on a GDI vehicle. The PCM charges a 65-volt capacitor for all injectors on a single circuit per injector. When the PCM wants to energize the injector the PCM simply ground-side controls each injector one at a time sequentially. Using a schematic on a GDI system you can identify an injector pair of wires by noticing the wires are twisted together. Both wires are labeled inj. ctrl. The reason being is that their magnetic fields oppose each other. In addition, the color-coding has some uniformity. For example, the 65-volt feed wire may be a solid purple while the ground side control wire may be purple with a white tracer. You may see another injector circuit with a solid brown wire for the 65-volt feed and a brown wire with a white tracer to ground side control the injector.
Let’s take a look at an amperage waveform on the bottom trace in Figure 19. Notice the peak current reached 12 amps and then went to hold at 2 amps. The total screen time is 5 ms. A total of 10 divisions means that every division represents .5ms. You can see that the amperage on-time measures .8ms. Now let’s look at a dual-trace voltage example in Figure 20. The top waveform is where the PCM supplies the GRD. Note that after the injector turns off the 65-volt spike, the injector on-time measures .8ms. This is identical on both channels.
Learning to navigate the use of a DSOs buttonology comes easy with repetition. This compares to the learning curve we had to go through when learning to navigate our cell phones or scan tools.
About the Author
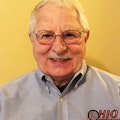