I was teaching a class in Montreal, Canada, that worried me as I was preparing the material. I have a lot of confidence in my abilities and also enough self-awareness on what I should stay away from. My apprehension wasn’t the subject manner. It was...is there enough to teach given this was a three-day class? I had been at this college before and knew most of the faculty.
The department head wanted a class on pure electric cars. This was some time in 2013. Once the fee was established and the date sent, I went to work writing an outline for the class. In no particular order, I listed all the components used in an EV that were similar in a hybrid vehicle. As this was my third visit, I had a good idea what they knew.
One by one, I added the EV side that related to the hybrid’s DC-DC converter, inverter, drive motor or motors, high voltage cables, detection systems for high voltage leaks, electric air conditioning compressors, li-ion cells, modules, cooling systems and more. I had never been asked for a class that excluded the internal combustion engine (ICE).
In 2013 hybrids were the dominate technology. I started my high voltage training company, ACDC, in the year 2000. A lone Honda Insight was the subject matter. As I made sense of this transition, I said in the classroom, “ACDC will make sure your 12-volt brain is well developed. Then we will create a high voltage brain to use along with it. Where the two brains match up, the learning is easy, but sometimes ACDC will break the connection between the two, so your 12-volt brain is not used on a high voltage system.”
We still use that thinking today. It is 2024 and the ICE is no longer needed, if a person, school, city or company wants to change fuel sources. In 2013, that possibility was very limited. Change was happening then but ever so slowly, from all ICE, to hybrids and now pure electric vehicles. In a technician’s lifetime, that change was fast. As a result we must change our diagnostic approach.
As the class in Montreal was getting closer, I removed all references in my handouts to hybrids. What was taken out? Nickel Metal Hydride chemistry, belt-driven anything (water pumps, A/C compressors), typical ICE cabin heating, all ICE and transmission lessons, and more.
What was added to make it an EV? Cells in parallel called groups, group balancing, SAE J1772 charging standard plugs, DC fast charging, more advanced cooling and heating systems for the battery packs, heating for the passengers, battery removal equipment, estimating range, the onboard charger, a gateway for high voltage distribution, water tight battery packs, module replacement at the pack level, and more.
Let us take a “no start” in a typical ICE-powered modern car or truck. In this case, the car gets towed in and the customer is not with the vehicle. This may be a new customer that does little preventive maintenance. You have no service records and the service advisor sold one hour of diagnostics. You are already in a tough position. The work order has only “No Start” written on it. This is the way the shop operates. It is not technician centered.
What do you do? If it is not snowing, raining or you don’t see a tornado heading your way, you grab four tools. In your bag you add a scan tool and a 12-volt jump box, most likely your own (that way you know they are both charged up). The other tools are an OBDII break-out-box and a DVOM. You get in and plug in your break-out-box into the DLC with the meter connected to pin 16 and 4. Before you try to crank the car over (KOEO), you check the voltage of the 12-volt battery. It reads 10.7-volts. No need to add more codes, so you locate the 12-volt battery. If you are lucky, once you open the hood, it is in plain sight. Attach the jumper box and get back in and gather any codes. Make a PDF of the codes. Now you try to crank over the engine. It cranks over and will not start.
Basics again. Fuel? Gauge says just over a quarter of a tank. Clear the codes and try to start again. No start. Read the codes it has generated. Shut it down, back in the shop looking up service information. The clock has been ticking and you have 25 minutes left. Ten minutes on the computer. Back outside for a general look at the entire car. Needs tires, oil is dark, cracked and missing part of the tail light lens. Wipers torn. The usual stuff. Back inside with the service advisor. Time is up. No need to push it into the service bay. You get another job to work on. Does this sound familiar?
In another shop, the diagnostic work can start with the customer coming over before the work begins with their service records for a discussion about their car, history and a quick look at the car while they are there. The one hour now can be used to sell the actual time and parts needed, just to get started. There needs to be a fee before the tech gets deeply involved. Once you know the car was recently purchased as a no start and sat for two years makes the job very different than a “no start” that happened yesterday.
Now let us replace that same scenario with an eight-year-old Nissan Leaf EV. Out the door you go with a scan tool, a 12-volt jump box, OBDII break-out-box, and a DVOM. Using your break-out-box you read 10.7-volts at the 12-volt. You locate the 12-volt battery under hood, connect the jumper box and get back in. Scan the EV for any codes in “Power-On” mode, the EV equivalent of KOEO. Make a PDF of the codes. Now you try to go into “READY.” No READY light. Range says just over 30 miles left. Clear the codes and try to start again. No READY. Read the codes it has generated. Shut it down, back in the shop looking up service information. The clock has been ticking and you have 25 minutes left. Ten minutes on the computer. Back outside for a general look at the entire car. Needs tires, cracked and missing part of the tail light lens. Wipers torn. Looks like you are in the same boat.
The technician and the service writer must get together and form an alliance on how to handle these situations. An old-fashioned system and new electric vehicles require a new approach. Once you are off to a better start, the triad (customer, shop and technician) must all feel that their concerns are understood. The success of the repair requires that all three parties have their goals met. The shop needs to make a profit. The customer will return the next time service is needed. The technician knows it will not come back for the previous concern as the root cause was fixed. How do we get there?
A three-way partnership
The technician ultimately does the work. The car owner is a partner in all this and they need to know that and should be encouraged to participate. That starts with a great website that explains what the shop needs from them. Set up a time to sit down with each new customer and get the information you need. It can still be in written form, but an electronic device will be faster for keeping records. Complete a history of their vehicle’s service, repairs, recalls, accidents, and the personal information they are willing to share. Make sure the tech has access to that data. Establish a realistic fee after a 15- to 30-minute interview and cursory look at the car. The tech can do a visual and scan check while the service advisor interviews the owner. “Who is the decision maker?” is a fair question to ask. Once the customer agrees to the fees and your process, he or she signs the work order and the real work begins. Up to this point, you have every reason to charge a fee for what I call “Intake and Inspection” to get the customer to join the triad or find another shop. At this point. sell a “comprehensive inspection.” This is for first time customers. It is a complete physical exam for a motor vehicle.
Depending on the condition of the electric car, the technician — armed with enough time and parts — can start whatever process make sense. One more tip here. The late Jim Linder, a great mentor to many (including me) taught us to use the word “analyze” rather than “diagnose” when writing up the work order or talking to a customer. The word explains what a technician is doing with their brain. When getting back to the owner after a “comprehensive inspection,” use multiple electronic work orders, and start with their primary concern. Then, in this order start with safety, emissions (if it has an ICE), reliability, progressive damage, performance, entertainment and lastly, cosmetics.
Let us go back to the Leaf. It was towed in. The customer’s spouse drops the kids with a relative and picks up his wife. They were told to bring what they have for service records and that they will need to remove their personal belongings from the car. They are at your shop now cleaning out their car. Yes, they will clean their junk out of the trunk if you ask them nicely.
How much better would this help the technician? These electric vehicles will not be easy to repair. Even with some great training, the list of what can keep an EV from going into “READY” is not the same as an ICE. No more getting the 12-volt starter motor to crank the ICE. No more spraying “starter fluid” in the intake. The list goes on. Where do you start? A history of the EV is worth the time. That “Intake and Inspection” fee is designed for that purpose.
In the intake process you need to know:
- Condition of overall health of the EV
- Salvage title?
- Bought at auction?
- How many owners?
- How long have they owed it?
- Are all the recalls done?
- Too much rust?
- Unsafe to drive (bald tires)?
- Most of the service records are brought in
- Was it worked on by someone else for the same problem?
- How cooperative is the owner?
- Are you equipped and trained for this job?
- Do you need to learn and this job will help?
Once the above questions have been answered, and the owner is willing to pay you to find out more, the technician is now ready to spend the time needed to look at this Nissan Leaf. It might be simple. The intake process will get this customer and their EV into your system.
I owned an independent Honda / Acura repair shop for over 25 years. The above system was realized after some trial and error. If you graduate from our two week class called “Up Your Voltage,” we offer tech support on HEV, PHEV and EV. There is a catch. You must get a history of the vehicle and the proper equipment must be at the shop to support the technicians.
Summary
If you are a technician that stays away from modern cars and trucks, this switch from ICE to EV will be very difficult. Most likely, you can stay busy for a long time, taking care of what you know. No problem with that.
On the other hand, a well-trained tech that loves to learn and finds new systems exciting, will love the future. Retraining your 12-volt brain is possible — no matter what your age.
Tools used
- 12V jump box
- Scan tool
- OBD-II break-out box
- DVOM
About the Author
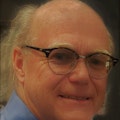
Craig Van Batenburg
Craig Van Batenburg is the CEO of ACDC, a hybrid and plug-in training company based in Worcester, Mass. ACDC has been offering high voltage classes since 2000, when the Honda Insight came to the USA. When EVs were introduced in 2011, ACDC added them to their classes. Reach Craig via email at [email protected] or call him at (508) 826-4546. Find ACDC at www.FIXHYBRID.com.