The evolution from HVAC to thermal management in EVs
HVAC (heating, ventilation, and air conditioning) has been used to describe what happens in the cabin to keep people comfortable while driving. We need to stop using that term and rename it “thermal management”, but that sounds too much like engineering. The truth is you are an engineer, albeit without a degree.
On my business card it says “Craig Van Batenburg, DMM”. That is not a reference to a Digital Multi Meter. DMM in this context is “Doctor of Moving Metal.” Don’t sell yourself short as you study these new EMVs (any vehicle with a high voltage drive system). These systems require the basic understanding of engineering, physics, and other subjects that many of us avoided in school so we could work “with our hands.” I enjoy “working” on mechanical things, but our brains must have critical thinking skills to figure out what went wrong. To do that, we must understand the systems.
When discussing heating, ventilation, and air conditioning in an EMV it takes on a whole new meaning. Not only are we using HVAC to cool or warm people and pets, it also plays a big part, either directly or indirectly, in keeping the HV battery, inverter, DC-DC converter, HV battery charger, fuel cell, electric motors, and other systems operating in a safe and efficient temperature zone. This article will explain the cooling and heating system’s “construction and function,” plus some unusual thermal systems used in EMVs.
Cabin Heating Systems
The traditional heater, according to our research, was invented by an American named Margaret A. Wilcox, who was born in Chicago in 1838. It was patented on Nov. 28, 1893. Wilcox’s patent directed air from over the engine for warming the passengers in the 19th century. This led to using coolant not long afterwards. Using wasted energy is smart. Wasting energy is not. As we all know an internal combustion engine (ICE) creates more heat than needed, so “free” heat was always a plus for any ICE-driven vehicle. I owned a 1959 VW Bus (Figure 13 1). The ICE was air cooled and the heater was a joke. It was a very cold ride in the winter. All ICE vehicles are liquid cooled, so heating those vehicles is easy.
When the first Prius was sold in Japan in 1997 (as a M/Y 1998), the heating system for passengers was pretty simple. The original Prius added a bypass hose with a 12-volt coolant pump that was controlled by the HVAC ECU. Once the heat was turned on by the driver, the ICE would stay on until the coolant temperature reached about 180 degrees Fahrenheit and then “idle stop” was enabled. If the Prius driver set the climate control to 72 degrees, the HVAC ECU would communicate with the Hybrid ECU and if the HV battery was over 50% SOC, the ICE would shut off at a stop. The 12-volt coolant pump would be turned on and hot coolant would now circulate in and out of the heater core with the in-line pump. The ICE used a belt driven water pump when the ICE was running. Many techs have asked us what happens to the cabin heat when the ICE is in idle stop? The answer can be found with a scan tool.
Here are the questions you need to answer:
- What is the reading of the ICE coolant temperature sensor?
- What is the SOC of the HV battery pack?
- At what SOC will the ECU restart the ICE?
- How much coolant temperature loss was there before the ICE restarted?
- Why did the ICE restart? SOC or cooling down during idle stop?
Once you have answered those questions you can come to some conclusions.
PHEV Systems
A plug-in hybrid has a more complex heating system than a hybrid vehicle. In order for a PHEV to function as an EV for short distances, the cabin heating does not use the waste heat from the ICE as the engine is not running. Some clarification here. Some PHEVs, like the Chevy Volt, have a powerful drive motor (111kW) and does not need the ICE at higher speeds or loads. The early Volt is classified a PHEV or an EV-ER, depending on its mode of operation. Other PHEVs, like the first Prius PHEV, had a drive motor half the size of the Volt. To keep up with fast moving traffic, the ICE will start when the driver presses the “Go” pedal all the way down. Most PHEVs rely on the ICE even when the HV battery pack has sufficient charge to power the PHEV. When PHEVs first came to market in North America, they all bought the same HV heater (Figure 13-2) from a German company, with various attachment points and connectors. To provide cabin heat, a 1-gallon container (ACDC estimate) of coolant was heated using the high voltage battery for power, and that hot coolant was circulated in and out of the heater core with a 12-volt pump. The Chevy Volt had a decreased driving range of 30% to 40% in cold weather, as the heater was using the only energy on-board, the HV battery pack. That old-fashioned technology was also used in the Ford Fusion/C-Max Plug-ins called Energi. The load on the battery was 5 to 7 kW. To stay warm is a human desire and in the beginning many early PHEV owners used the heated seats and heated steering wheel, while wearing a jacket, hat and gloves, to stay warm with the heat off or on low to gain more range. That was not the solution most drivers wanted!
The original Chevy Volt started the ICE at 25 degrees regardless of the HVAC setting. Even if the driver kept the heat off, the PCM commanded the ICE on to use the warm coolant in the ICE and a “mixing valve” would add the warmed ICE coolant with the separate cabin heater coolant. Drivers complained to GM and a few years later the driver had the ability to have the ICE stay off until it reached 15 degrees, but then the ICE would start, even if the battery pack was fully charged. Once the SOC of the HV battery was at a pre-determined low level (usually 20% SOC or less), the ICE would start and the waste heat of the combustion process would provide all the free heat required.
More About the Volt
On the first generation of the Chevy Volt M/Y 2011-2015, the engine cooling system and cabin heater worked together. It had an ICE radiator (No. 1), surge tank (No. 2), a 12-volt electric coolant heater pump (No. 3), high voltage (HV) coolant heater No. 4), a cabin-mounted heater core (No. 5), a coolant flow bypass valve (No. 6), belt-driven water pump (No. 7), an ICE (No. 8) and a Thermostat (No. 9). The ICE coolant flow bypass valve (No. 6) is controlled by the Hybrid Powertrain Control Module (HPCM2) to assist in regulating the cabin HVAC system, based on the availability of engine heat from the ICE. The coolant bypass valve separates the ICE and the cabin heater coolant loops to prevent heat generated by the HV coolant cabin heater from losing its heat into the ICE coolant system when driving in EV mode. The coolant flow bypass valve (No. 6) has two positions. When the ICE is OFF (as during electric-only EV operation) the valve is commanded to be in ICE bypass mode, shown as Position “A.” This permits the electric pump to circulate coolant through the HV heater then through the heater core in a short, efficient loop. For maximum electrical efficiency, feedback from temperature sensors in the passenger compartment and heater coolant loop are used to determine the necessary amount of electric current applied to the HV battery heating element which is an integral part of the Coolant Heater Control Module (CHCM). After the ICE starts up, in extended range mode for instance, additional ICE heat will soon become available to assist the HV coolant cabin heater in warming the passengers. At that point, the flow control valve is commanded to the “linked” position, shown as position “B”, and the two coolant loops are then connected. This parallel connection permits the sharing of coolant between the ICE and heater core, and subsequently the HV battery heating element (CHCM) power level will be reduced and/or cycled OFF/ON as the ICE turns on/off during extended range (charge-sustaining mode) operation in order to keep the cabin warm.
The ACDC Chevy Volt shows “Engine Running Due to Temperature.” In this case the Volt has 26 miles left in EV mode, but the ICE is running to provide additional cabin heat. Whenever the ICE is ON, a conventional belt driven water pump (No. 7) is used. The thermostat (No. 9) regulates the normal ICE operating temperatures in a conventional fashion, but can be heated electrically to speed opening and regulate flow. The thermostat creates a flow restriction for the ICE cooling loop that promotes a positive coolant flow and helps to limit air cavitation. When the ICE is first started and the thermostat remains closed, a hot water bypass hose permits heated coolant flow to the electric pump and heater core. Once the thermostat opens, flow will be permitted through the radiator which will maximize cooling yet still allow flow through the heater core loop for cabin heating. This system is complex and not easy to service, but the idea was to get the maximum range from a small battery pack in cold weather.
EV Heat Pumps
When the first modern electric vehicles came to market, the Mitsubishi i-MiEV and the Nissan Leaf, the old-fashioned technology of heating the cabin by warming coolant the way a PHEV did, lasted just a few years. Nissan, in M/Y 2013, came out with a “heat pump” in the SL and SV trim levels of the Leaf. This improvement in cabin heating reduced the load on the battery from 5-7 kW to 2 kW, for the same amount of heat. This allowed the EV to go farther on a charge while keeping the occupants comfortable.
How does a heat pump work? In simple terms, the condenser and evaporator change places by adding another expansion valve before the condenser. Then more tubing was added to bypass each expansion valve and the computer, depending on a request for heat or cooling, used one expansion valve or the other. In this way the heat is then produced in the cabin as you try to cool the air outside the vehicle.
Heat pumps have been used in buildings since the 1940s, but the concept goes back to the mid-1850s. When Nissan installed their version of a “heat pump,” it was not used on the base model. At mid-year in 2013 the Leaf “S” had the heat pump. A couple years after Nissan added the heat pump to the Leaf, Kia added a “tweak” to make it more efficient. Toyota (Denso) then improved it again the next year.
Why all the improvements so fast? Consumers wanted more range in cold weather.
As we move away from the belt-driven compressor and more waste heat from internal combustion engines, a new landscape will emerge. Heat from a high voltage pack after the EV is shut off can be used to keep the cabin warm. A refrigerant cooling system and be used along with a liquid cooling system to move heat and cold around the EV where it is the most useful. Rather than add a high voltage grid under the dash, the electric drive motors can be run in a less efficient manner to make waste heat to warm the cabin on a cold day. That and more is being done today to not only keep the passengers in a climate-controlled cockpit, but also make the best use of the electricity that charges up the vehicle. Good thermal management of the electric vehicle is also good management for our earth.
About the Author
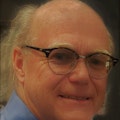
Craig Van Batenburg
Craig Van Batenburg is the CEO of ACDC, a hybrid and plug-in training company based in Worcester, Mass. ACDC has been offering high voltage classes since 2000, when the Honda Insight came to the USA. When EVs were introduced in 2011, ACDC added them to their classes. Reach Craig via email at [email protected] or call him at (508) 826-4546. Find ACDC at www.FIXHYBRID.com.