Today’s steering systems are designed to maintain the correct wheel alignment for optimal tire-to-road contact while minimizing tire wear and still being able to adapt to variable road conditions for improved handling and stability. But the steering system hasn’t been the only concern of the automotive manufacturers. There has been a proliferation of active suspension systems, integrated with sophisticated sensors and electronic controls that adjust in real time and provide an unprecedented level of comfort and control while driving.
Active or Adaptive Suspension Controls: the Differences
Suspension systems have evolved significantly beyond their traditional role of simply providing a smooth, comfortable ride. Modern innovations now integrate adaptive and active controls, allowing vehicles to respond dynamically to changing road conditions and driving demands. These systems not only focus on comfort but also enhance handling, reduce body roll, and maintain optimal ride quality. Some manufacturers are incorporating adaptive or active suspension variants, or a combination of both on their vehicles — all to improve overall vehicle performance and stability.
The key difference between adaptive and active suspension systems lies in how they adjust to road conditions. Adaptive suspensions adjust the ride height in response to real-time road feedback or driver input, while active suspensions use electronic controls to manage vehicle height and proactively control body roll and stability. To address the limitations of a one-size-fits-all approach, many manufacturers combine both systems, offering enhanced adaptability and performance across a wider range of driving scenarios. Active suspensions will often use bi-state, tri-state, continuous, or magneto-rheological damping control in the struts or shocks to control ride quality and body roll (but for this article we will concentrate on the adaptive suspension system).
The adaptive suspension system is used primarily to control the vehicle ride height, but it can be used to control stability as well. The most common adaptive suspension version uses air springs to keep and control ride height. But there are hydraulic versions: Mercedes Benz S-Class and the BMW 7 series use a hydraulic adaptive/active suspension. This system controls ride height, damping force and body roll, hydraulicly. But these systems are relatively rare.
The air ride adaptive suspension is the more common version, and its name will depend on the marketing of the system by the manufacturer. Ram calls their system “Active-Level Four Corner Air Suspension.” GM calls their system “Air Ride Adaptive Suspension.” Ford has the “Adaptive Air Suspension” and Tesla has the “Smart Air Suspension.” Input information from vertical and lateral accelerometers, suspension position sensors, air pressure sensors, steering position and other pieces of data are sent either directly or via a network to the suspension controller for proper operation. The controller will then send out the needed commands to either the air spring control valve assembly or air spring to satisfy the required or requested driving conditions.
Adaptive Suspension Issues and Concerns
Compressor failures, air spring failures, airline leaks, and corrosion are the most common issues. Warning lights, DTCs and sagging tilted vehicles are a common issue. A good thorough visual inspection and a full system scan will often point to the issue when dealing with these systems. When looking at a failed Ram air ride system there are four common failures that we look at first: the 40-amp compressor fuse being blown, the compressor relay, a seized compressor and soapy water looking for air leaks. Another common Ram or Jeep air suspension issue is that the vehicles will revert to “plant mode” and disable the filling of the air bags. When this happens the vehicle will stay low and have a C2212:00 DTC set in the Air Suspension Control Module (ASCM) that can't be cleared. The common fix for this condition, after all the proper repairs are completed, is to use the scan tool and follow the filling from reservoir procedure. Typically, you only have to fill one corner, and this should take it out of plant mode and raise the vehicle to the correct height when the engine is started. Ensure all the doors and the tailgate are closed when doing this procedure. Another Ram tip is resetting the system. This is done with the ignition on, engine off. You will then press and hold the air suspension button for 40 seconds, and the system should recalibrate itself.
When working on or servicing the suspension on these systems, following the OEM service procedure is imperative, as many of these systems will hold residual pressure and that pressure may need to be relieved before service to prevent injury or damage. Both GM and Ram have special procedures to reset or learn the automatic level trim heights. Newer GM SUVs equipped with the automatic level control have a 13-step procedure to reset the learned trim height after a suspension position sensor is replaced or removed. It involves careful measurements in millimeters and that value will have to be entered into the scan tool as part of the procedure.
And once any repairs have been performed on the system, it may need to be refilled with nitrogen. This is a part of the air ride service that often gets missed, but the system needs to be filled with nitrogen to prevent any internal corrosion that compressed shop air may contain. Again, following the OEM service procedures can’t be stressed enough.
When performing an alignment on these air-ride-equipped vehicles, technicians need to pay attention to the settings of the suspension system. The evolution of suspension technology has also led to the development of unique alignment procedures tailored to specific vehicle designs. GM and Ram have an Alignment Mode, Tesla uses Jack Mode, which must be entered into before doing an alignment. Alignment mode can be entered into using the dash or center information stack or the scan tool, and once entered the vehicle's suspension system will move the vehicle to the correct position. This will optimize the vehicle’s height to provide the most accurate wheel alignment, and this mode should be enabled once the vehicle is driven onto the alignment rack. Manufacturers like Toyota and Ford emphasize post-alignment recalibrations to ensure their Advanced Driver-Assistance Systems (ADAS) components function seamlessly.
The Modern Steering System
With all the technological changes that we technicians see on today's vehicles, the three fundamental steering angles (camber, caster, and toe) and the steering geometry angles (steering inclination angle, scrub radius, included angle, and thrust angle) are important to understand. These steering settings and angles, some of which are adjustable and some of which are not, are vital to proper vehicle steering, safety, and driveability.
Examining the Adjustable Angles
Camber is the tilt of the wheel when viewed from the front or rear. It can be either positive (tilted out at the top) or negative (tilted in at the top). The camber setting optimizes tire contact with the road for various driving conditions. Negative camber enhances cornering grip by maintaining the tire's contact patch during turns. However, too much negative camber can lead to uneven tire wear and instability on straight roads. Positive camber has the top of the wheels tilting outward. Positive camber is uncommon on today’s vehicles and may result in poor cornering stability and uneven tire wear.
Caster is the tilt of the steering axis as seen from the side of a vehicle. Positive caster means that the top of the steering axis tilts toward the driver (rearward), whereas negative caster tilts it away (ahead). Positive caster is widely used because it improves straight-line stability, steering feel, steering self-centering, and better cornering performance. Negative caster reduces steering effort, but it sacrifices stability and can lead to wandering, poor cornering, and reduced vehicle control. While caster does not directly impact tire wear, excessive positive or negative caster can indirectly contribute to tire wear by causing misalignment in other suspension components or uneven weight distribution during turns.
Toe refers to the angle at which the tires point in relation to each other when viewed from above. Toe-in occurs when the front edges of the tires point inward, while toe-out occurs when they point outward. Proper toe settings ensure that the vehicle handles properly and maintains stability. A toe-in setting is often used on vehicles to counteract the natural tendency of the tires to spread outward under acceleration, especially in front-wheel-drive vehicles. A toe-out setting on the other hand, is sometimes utilized on high-performance vehicles to enhance cornering response. Improper toe settings can significantly impact tire wear and often make the vehicle feel unstable or uneasy, which affects both straight-line tracking and cornering performance.
The Nonadjustable but Critically Important Angles and Measurements
Steering Axis Inclination (SAI) is the angle formed between the steering axis and a vertical line when viewed from the front or rear of the vehicle. This angle is built into a suspension design and cannot be adjusted. SAI helps return the wheels to a straight-ahead position after turning, improving stability and steering control. Scrub radius, on the other hand, is the distance between where the steering axis meets the ground and the tire’s centerline. Both SAI and scrub radius influence how the vehicle steers, handles, and how the tires wear.
The relationship between SAI and scrub radius is important because they work together to determine steering characteristics. For example, a positive scrub radius (when the tire centerline is inside the steering axis) can cause issues such as toe-in and instability or darting when braking. A negative scrub radius (when the tire centerline is outside the steering axis) can lead to toe-out and potential instability while driving.
Any changes or deviations in SAI or scrub radius may indicate suspension damage or a bent component, which often goes unnoticed to the naked eye during a visual inspection. SAI and scrub radius are critical for ensuring proper steering stability and tire wear, and provide valuable diagnostic insights during an alignment to detect suspension damage or misaligned components.
The included angle is the sum of the SAI and camber angles, forming the angle between the tire’s centerline and the steering axis. It plays a critical role in vehicle alignment diagnostics, as deviations often signal issues like cradle misalignment or damaged suspension components. Alignment machines measure this angle, and it should be consistent between the left and right sides, typically within a half-inch (12.7mm). If the included angle difference exceeds 1.5 degrees, it shows potential suspension damage. These variations directly affect steering stability, tire wear, and overall drivability, and highlight how the included angle is an essential diagnostic tool for maintaining proper vehicle handling.
The last critical angle that we will look at is the thrust angle, but we will include setback as a measurement here as well. The thrust angle refers to the angle or difference between a vehicle's geometric centerline and the direction in which the rear wheels are pointed. It plays a key role in ensuring the vehicle tracks straight and handles properly. A misaligned thrust angle can result from issues such as bent axles, damaged frames, shifted rear cradles, worn suspension components, or improper rear toe settings. Symptoms of an incorrect thrust angle include off-center steering, vehicle pulling, dog tracking (where the rear end appears offset), crab walking (moving slightly sideways like a crab), and uneven handling. Modern alignment equipment is used to measure and adjust the thrust angle, particularly in vehicles with adjustable rear suspensions. For non-adjustable suspensions, the front wheels can sometimes be aligned to compensate. A proper thrust angle is essential not only for stable handling and tire wear but also for maintaining the accuracy of ADAS, which relies on precise alignment with the vehicle’s travel direction.
A thrust angle reading under 0.25 degrees typically means nothing is bent or damaged, while higher readings on a live rear axle (cradle type) can point to shifted frame mounting points. Setback is the distance (from the wheel center) that one front wheel is further back from the other. This measurement can highlight frame or suspension damage, such as bent control arms or worn bushings. Misalignment in thrust angle and setback may signal frame damage, like a "diamond frame," where one side rail has shifted and affected suspension mounting points. Alignment checks, especially after an accident, can be used for finding thrust angle issues, particularly in all-wheel-drive vehicles, with rear cradle suspensions. Typically, most thrust angle problems can be corrected with toe adjustments, but a shifted cradle might limit those adjustment possibilities.
The four-wheel alignment is the most accurate alignment procedure. This includes aligning the rear wheels to the vehicle’s geometric centerline and thrust line and then aligning the front wheels parallel to the rear wheels. The process ensures best handling, even tire wear, and proper tracking of the vehicle. Using a modern alignment machine, technicians can diagnose irregularities, identify damaged or shifted components and make changes thanks to the accurate measurements these machines provide.
As vehicles continue to evolve, so will suspension and steering systems, but the essential steering angles and settings are still there and as important as ever. Future advancements are likely to focus on even greater integration with vehicle control systems, improved energy efficiency, and enhanced durability. For now, the shift toward electronically controlled and adaptive suspension systems represents a significant leap forward, providing drivers with unparalleled comfort, safety, and performance. Whether managing the complexities of ADAS integration or refining the ride quality of luxury vehicles, modern suspension systems stand as a testament to the power of innovation in automotive engineering.
About the Author
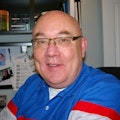
Jeff Taylor
Jeff Taylor is a seasoned professional at CARS Inc. in Oshawa with 40 years in the automotive industry. As a skilled technical writer and training developer, he holds licenses in both automotive and heavy-duty vehicle repair. Jeff excels in TAC support, technical training, troubleshooting, and shaping the future of automotive expertise.