I have been working in the automotive repair industry for nearly 50 years. When I started, the typical industry title for my job was “mechanic”. Since I started on this career path, the job description, along with the title, have changed many times. As a “mechanic”, your role was to determine what was wrong with the mechanical aspects of a vehicle, which was typically based on the symptoms presented combined with your experiences on like vehicles. Once you determined what was wrong, you repaired or replaced the faulty mechanical components and the vehicle was back on the road. The mechanic title later changed into “installers,” as we would install parts that failed or went beyond their service life. Now, thanks to the addition of enhanced technology and computer systems, we have turned into “technicians.” We are capable of performing complex diagnostic routines both to determine where the problem lies and how to repair the electronic and mechanical components when needed.
Despite these waves of change, one thing that has remained a constant throughout every phase of my career has been my reliance on quality hand tools. When I started in the business, mechanics were required to supply their own tools. At that time, since most shops primarily worked on domestic vehicles, the need for hand tools was limited to a set of SAE sized tools without the need for metric sizes. If you did see the occasional Volkswagen Beetle, Mercedes, or Datsun, you either borrowed the tools from someone or did not accept those jobs until you saw enough cases to justify buying the tools.
As vehicles became more complex and additional systems were added, hand tools evolved into more “specialty tools” designed to make a specific task easier or faster. In some cases, they made repair possible. At this point in time, a technician’s tool box needs to include complete sets of both SAE and metric wrenches and sockets, in addition to basic tools like ratchets, extensions, pliers, screwdrivers, and a large assortment of specialty tools that are used for specific tasks to facilitate and expedite the repair process.
I am an owner and crew chief of a drag race car as well as four others, including a five-engine tractor used for pulling. In this article, we will discuss a variety of hand tools my team and I use to make jobs simpler and quicker. I stress quicker because the race car we will be showcasing is known as a Top Alcohol Funny Car that we campaign in the NHRA circuit. This car is capable of running the quarter mile track in about 5.4 seconds at around 270 MPH. My crew of five people is capable of completely rebuilding its 3500-horsepower machine and replacing the clutch in roughly 40 minutes.
This is accomplished by a combination of a group of people that are trained to do very specific tasks, an engine that is designed to be serviced quickly, and some of the best hand tools on the market that are built to perform tasks quickly and efficiently. Whether you’re working on a race car or a production car in a shop, speed, and efficiency will not only set you apart from others, but make you more profitable.
We will start by grouping hand tools into three groups: essential, task specific, and time saving.
The must-haves
Essential hand tools are the ones you’ll find in almost every toolbox, whether in a shop, your home garage, or in a race pit. These tools usually consist of a set of combination wrenches in either or both metric or SAE sizes, ratchets and extensions of various sizes, sockets, both deep and shallow, and numerous pliers, screwdrivers, hammers, chisels and punches.
When you’re looking to purchase sockets, you’ll typically buy a six-point socket that provides a lot of surface area on nuts and bolts. This can assist in breaking loose stubborn fasteners without slipping. When working on our race engines, we typically work with a twelve-point high quality fastener, which requires a twelve-point wrench or socket. The twelve-point design performs two functions: the head of the nut or bolt is smaller in order to fit tight areas, and they are very strong so they will not round off. Since these fasteners are mostly twelve-point, all our wrenches and sockets must be twelve-point as well.
The ratchets and extensions we use are what you’d typically find in almost any other toolbox, with the addition of flexible ratchets and wobble extensions that allow access in some tight quarters.
The task specific
Some of our task specific tools include Allen sockets, both in a straight and ball design. The straight sockets are solid and are used when loosening or torqueing an Allen head fastener to its specification. We use the ball design Allen sockets to allow access in areas that will not permit a tool to be used straight on the fastener. Using these ball end sockets allows users to utilize either a ratchet or a power tool to speed the process up, even when there are obstructions preventing the use of a straight socket.
Other task specific tools are the KNIPEX CoBolt cutter that we use to cut the stainless-steel cable that is used for our parachute. KNIPEX Cobra pliers are also useful to make sure fasteners are secure after a last-minute adjustment of the wheelie bar at the starting line. We also use the KNIPEX electronic cutters to snip cable ties. These cable ties are used throughout the car to secure wires and hoses. The electronic cutters will snip off the excess length of a cable tie without leaving a sharp edge, therefore leaving the cut end safer for the crew. We have many more task specific tools, but many of them fit into the time saver category as will.
The time savers
As for the time saving tools, we’ll start with the Milwaukee brand electric driver tools we use. In the past, we’ve used air tools to speed up the process of removing fasteners, but with the emergence of high-speed, high-power battery electric tools, we’ve switched over to Milwaukee for a faster process overall. They all use the same battery, and using a charger that juices up six batteries at a time ensures we always have enough power for every tool. We use a pair of 3/8” drive impact drivers, a 1/2” impact driver and a 1/2” reversible drill. In addition to these tools, we use a leaf blower, a small shop vacuum, and some LED work lights, all of which use the same battery pack as the impact drivers. Electric tools mean there are no air lines lying on the ground which can cause a tripping hazard.
One of my favorite time savers is a flexible ratcheting box wrench. We have multiple sets of the GearWrench brand. These tools allow access to nuts and bolts from multiple angles and are used similarly to a ratchet and socket but with a much smaller face for use in narrow areas. This makes removing and installing cylinder head fasteners located above the lifters on our race engine a snap.
Where’d that 10mm go?
Tool organization is a key part of being fast and efficient. Since we have such little time between runs on this car, we find it necessary to have a duplicate set of tools for each side of the engine, another set for under the car to perform maintenance on the crank and rods, and another set for removing the transmission and clutch assembly. Each workstation has the tools necessary for the task at hand along with a few others for a variety of situations.
We have many specific tools we use to measure clearances throughout the each car. Each of these high-quality dial indicators, calipers, and torque wrenches are handled with care, but are also sent out regularly to test and verify their calibration. Over the years I have found that many technicians end up creating their own problems by not maintaining their tools. Think about this: If a torque wrench is out of calibration by as little as 5 percent, when it’s used to torque a connecting rod to 125 lb/ft, you could either be overtightening and stretching the rod bolt by as much as .003” or leaving a rod bolt loose. Either way, there will be engine damage when the engine operates at over 10,000 RPM.
Safety first
Lastly, I need to mention tool safety. Some of my pet peeves include seeing a technician using dirty or oily tools. This can cause the technician to lose their grip on the tool and injure themselves. Using tools in ways they weren’t designed for, such as a screwdriver used as a prybar, is also a bad idea. My least favorite thing to see is a technician using a ratchet or wrench with their fingers wrapped around the tool. I know tool makers have made great efforts to make their tools comfortable in your hand, but wrapping your fingers around the tool when you are breaking a fastener loose will cause injuries if the wrench slips. Since there’s no protection around your hand or fingers, if a slip happens, your fingers will be between the wrench and whatever part on the car is stopping the wrench. My advice is to use the palm of your hand to push the wrench. That way if it slips, the wrench will hit the obstruction and not injure your hand.
Hand tools may seem to be a simple topic, but the right tools for the right job will make your life easier, and in many cases, your jobs more profitable. See you at the races.
About the Author
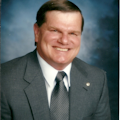
Barry Hoyland
Barry Hoyland has been in the independent aftermarket for more than 45 years as a technician, technician instructor, shop owner, and shop management consultant. He owned and operated a successful Southern California automotive repair center that offers complete auto care and specialized in emission and diagnostic services for over 28 years. Hoyland also owned a company that modified vehicles to perform as emergency response units and mobile command centers, incorporating high-end electronic components into today’s vehicles. Hoyland has experience with all size and types of vehicles including traditional gas, hybrid electric, alternative fuel, and heavy duty diesel trucks.
Hoyland has provided consulting services for many automotive shops, fleets, and government agencies in order to improve their operational efficiencies.
In addition, he has worked with many NHRA drag racing teams as a crew chief on supercharged alcohol and nitro-methane fueled cars and currently serves as a crew chief on a Top Alcohol Funny Car, a Nostalgia Funny Car, and a Nostalgia Alcohol Dragster
Hoyland holds certifications in ASE: A1, A6, A8, and L1, MACS 609, maintains a California Advanced Emission license, and a CDL with endorsements for double and triple trailers, tankers, and HazMat.
When he is not helping to run a shop in the Pacific Northwest, Hoyland travels across the U.S. as an instructor of technical and shop management courses, many of which he has developed.