Hybrid electric vehicle (HEV) nickel-metal hydride (NiMH) battery service or replacement is a topic often written about or discussed in the automotive trade magazines today. Specifically, many of the discussions focus on the proper analysis, diagnosis, rebuilding or conditioning of the HEV battery pack. There also is high interest in how to determine the quality of the battery packs being offered by commercial rebuilders or where to purchase them.
A conditioned battery pack is defined as a battery that has had its NiMH modules balanced and capacity increased through the use of a cycling process, or lithium ion battery capacity recovered through basic cycling. However, in the conditioning process, no battery modules or other supporting components are replaced. Within the conditioning process the battery modules will be cycled. Cycling is a meticulous process of discharging the battery modules to 0 percent state-of-charge (SOC) and recharging them to 100 percent SOC to determine the current energy capacity and recover its (NiMH only) overall energy capacity capability. NiMH battery modules might need to be cycled two to four times to recover or “grow” the battery module capacity. The conditioning or cycling process can typically recover a battery module to 88 to 95 percent of its rating when it was new. Conditioning will not recover battery module cells that have been damaged by over-temperature, over-charge, electrolyte leakage or over-discharge, but it might recover capacity in batteries with long stand-time (i.e. long storage time).
All battery packs in this study were removed due to faults reported by the vehicle’s Controller Area Network (CAN) to the battery controller. However, it should be noted that the battery controller is only capable of triggering a CAN fault message if there is a gross battery pack or battery module failure through using dynamic direct measurement of battery pack or battery module terminal voltages. Battery pack energy (capacity) or state-of-charge percentage (SOC) is a complex software calculated value that is not directly measured. It can vary from 2 to 15 percent, depending on vehicle operating variables such as drive cycle (highway or city), ambient temperature, geographic location, terrain, and frequency between drive cycles (stand time).
The SOC percentage value also can become skewed as mileage increases. However, skewed (inaccurate) SOC percentage is not reserved for only high mileage vehicles. Depending on operating variables (mentioned earlier), AR&D has tested battery packs with less than 50,000 miles and model year ages of less than four years with severely depleted capacity (SOC percentage) without battery pack or module DTCs. Any battery pack with reduced energy (or power) capability also can cause vehicle fuel economy and acceleration performance to degrade significantly during its service life.
As an example, vehicle owners that have had battery conditioning or rebuilding at The Hybrid Shop dealer network that reported combined city/highway fuel economy numbers of 46 mpg when their vehicle was new also reported 33 to 35 mpg after five or more years of driving. Fuel economy numbers after battery pack conditioning/rebuilding are derived from customers using their usual drive cycle, gallons of fuel/fill, and number of miles driven as the data points. None of the owners report intermittent or hard fault DTCs (history or current faults) while their fuel economy numbers were decreasing over time. It should be noted here that none of the owners changed any other vehicle metrics after their batteries were serviced (i.e., tire pressure, engine, ignition system, fuel system or filters).
What does the aforementioned information have to do with a case study? The answer is relevance. First, the case study results mirror and support the AR&D historical data/experiences that have been documented on customer battery packs in past years. Second is applying the case study data to aftermarket battery pack rebuilders and/or distributors of rebuilt battery pack systems. Specifically, technicians might be relegated to relying on suppliers that may or may not have the expertise to properly test, analyze or repair the battery pack modules or related systems. The case study will assist many readers in knowing what specific metrics to consider asking their suppliers before making an expensive battery pack purchase.
Case Study Testing and Metrics Background
Testing Location: Automotive Research & Design, LLC (AR&D) Manufacturing / Research & Development facility – Port Angeles, Wash.
Test Engineer: Dr. Mark Quarto
Test Metrics: Based on Department of Energy (DOE) and United States Advanced Battery Consortium (USABC) testing metrics
Date Range of Testing: May 2013
Number of Battery Packs in Study: Three (3)
Battery Pack Types: Toyota Prius / Generation II (2004 to 2009)
Battery Pack Model Year and Mileage Range:
Sample 1. 133,067
Sample 2. 121,260
Sample 3. 80,436
Battery Pack Amp-Hour Rating: Rated = 6.5 (Actual = 5.76 – 6.0 Discharge Rate Dependent: DOE, AR&D test results)
NiMH Battery Cell Testing Criteria: 1.5 Volts @ 100 percent SOC / 1.0 Volts @ 0 percent SOC
Battery Pack Kilowatt Rating: 21kW (DOE and AR&D test results)
Ambient Temperature and Humidity: Temp = 18°C (65°F) – Humidity = 65 percent
Battery Discharging Metrics:
Test Device: AR&D Generation III Battery Discharger Unit
Software Controls: Proprietary AR&D Control Software
Power Test: ≈15C rate (based on DOE and USABC Hybrid Pulse Power Characterization – HPPC Test Metric)
Energy (Capacity) Test: C/1.5 rate (C = Capacity)
Battery Module Temperature Monitoring: Thermal Imaging – FLIR I7
Battery Charging Metrics:
Charger Unit: AMETEK XG-600 with modified connection cable system
Charger Controls: Proprietary AR&D Control Software
Charge Rate: Proprietary Stepped Algorithm C/2.5 – C/6 (C = Capacity)
Battery Module Temperature Monitoring: Thermal Imaging – FLIR I7
Battery Cooling Metric: 1200 CFM Air Blower
The case study battery packs provided to AR&D had less than 60 days of time since removal from a vehicle. Therefore, capacity loss due to self-discharge is negligible (≤ 1 percent amp-hour loss/month at ≤ 50 percent SOC) for a Panasonic prismatic battery module. In a Toyota Generation II Prius battery pack, the battery pack contains a total of 28 battery modules. Each module contains six battery cells rated at 1.2 volts/cell or a total of 7.2 volts (50 percent SOC) nominal voltage. The 7.2 volt modules are connected in groups of two modules or voltage (“V”) blocks for a total of 14.4 volts nominal per V-Block for a total of ≈202 volts dc. Therefore, when testing the battery pack modules, the testing will be performed by testing the 14 V-Blocks. In the event that one of the two battery modules in each V-Block is not performing, it easily can be monitored and identified during testing to determine that it is under-performing.
Sample 1 Prius Battery Pack
Sample 1 battery pack was tested with 133,067 miles. Because the total battery pack amp-hour counting data was not available from battery pack controller CAN data, actual amp-hour data is not known. The total capacity on the initial energy capacity test was < 0.15 hours. What this means is that the battery pack capacity was severely depleted.
The remaining 12 V-Blocks, if used in the same battery pack, would provide good energy production resulting in good vehicle performance. The key to rebuilding an excellent battery pack is to maintain < 5 percent variance between V-Block energy capacities with no variation in terminal voltage. A good battery pack will possess a ≥5 percent but ≤ 10 percent variance in V-Block capacities and less than 5 percent variance in terminal voltages. At this point, the cycling process has not been finished, but it also can be seen that there are two channels that have near the capacity of the cluster of battery modules. These two V-Block groups have good capacity but, notice that the terminal voltages are much lower than the group cluster. The voltage of these two channels drops to ≈1volt lower than the major group cluster before 0.25 amp-hours has elapsed. This is indicative of major cell damage that cannot be recovered by cycling the modules any further. Though this battery pack has failure of the two V-Blocks, the energy (capacity) in the remainder of the battery modules can be recovered and reused.
Sample 2 Prius Battery Pack
Sample 2 battery pack was tested with 121,260 miles. As with Sample No. 1, the total battery pack amp-hour counting data was not available from battery pack controller CAN data, actual amp-hour data is not known. The total capacity on the initial test was < 0.15 hour. What this means is that the battery pack capacity was severely depleted. Based on AR&D Toyota Prius battery pack performance experience, the vehicle in which the battery pack was removed would have had significant fuel economy reduction and poor acceleration performance. The voltage cut-off level for each of the battery module groups was reached very quickly and was low during discharging. However, despite the low terminal voltage of all battery modules, three of the V-Block channels extended their energy capacity from ≈0.40, 0.90 and 1.15 amp-hours respectively. It also should be noted that the channels with extended energy capacity also show a lower terminal voltage than the other channels after the initial loading of the battery modules. This is indicative of internal cell failure.
The key to rebuilding an excellent battery pack is to maintain < 5 percent variance between V-Block capacities with no variation in terminal voltage. A good battery pack will possess a 5 to ≤ 10 percent variance in V-Block capacities and less than 5 percent variance in terminal voltages. The cycling process has not been finished, but it also can be seen that there is one V-Block Channel that has approximately 2 volts less than the major cluster of V-Block module groups with only ≈0.25 amp-hours has elapsed. This is indicative of major cell damage that cannot be recovered by cycling the damaged module in this V-Block any further. Though this battery pack has failure of the one V-Block the energy (capacity) in the remainder of the battery modules has significantly recovered and can be reused.
Sample 3 Prius Battery Pack
Sample 3 battery pack was tested with 80,436 miles. As with Samples Nos. 1 and 2, the total battery pack amp-hour counting data was not available from battery pack controller CAN data, actual amp-hour data is not known. The total capacity on the initial energy discharge test was extremely varied but, scored at 3.70 amp-hours. However, by reviewing the data the battery pack capacity was good numerically but, the variances between the V-Block Channel groups was significant.
After completing two cycles (three discharges), the V-Blocks have recovered significant energy capacity. However, there is a capacity gap between all of the channels (excluding Channel 12). The energy capacity gap ranges from ≈1.40 to 1.65 hours (≈4.9 to 5.77) amp-hours. This resulted in a 16 percent variance between V-Block capacities, which results in a battery pack that possess an unacceptable unbalanced state (i.e., > 10 percent). This energy capacity variance can (in most cases) be reduced or “tightened” and capacity increased to its maximum by additional battery module cycles.
So, What’s Next?
At this point in the testing, let’s step back a moment to summarize each battery pack condition and determine the next steps. Sample 1 has 12 of 14 V-Blocks that are providing acceptable ranges of energy capacity, with three V-Block Channels that are providing excellent energy capacity. There are two V-Block Channels that have failed to provide the necessary voltage levels and should not be considered for use in rebuilding a battery pack. Sample 2 has excellent energy capacity on all but one V-Block channel. Sample 3 has good capacity in most of its V-Block channels and one channel that has failed to provide the requisite voltage level and should not be considered for use in rebuilding a battery pack. Therefore, none of the three battery packs could be considered for service in a customer vehicle to provide any measure of performance.
Sample No. 1: Serves as the “donor” for Sample 2 and 3 battery packs
Sample No. 2: Remove and replace V-Block No. 9 with donor modules from Sample 1
Sample No. 3; Remove and replace V-Blocks No. 11 and 12 with donor modules from Sample No. 1 battery pack
Rebuilding and Conditioning Results
The non-performing battery module V-Block groups in Samples No. 2 and No. 3 have now been replaced with the best performing V-Block module groups from Sample No. 1 donor battery pack. This was accomplished by disassembling the Sample No. 1 battery pack, removing the high performing modules and inserting them into Sample No. 2 and No. 3 battery packs. After Sample No. 2 and # No. 3 battery pack rebuilds were completed, these two battery packs were cycled one additional time to determine the final energy capacity and enhance overall balance of the 14 V-Blocks. The final energy capacity discharge graphs and data files indicate excellent capacity and balance for both Sample No. 2 and No. 3. Each battery recovered ≈91 percent (of new) energy capacity, with Sample No. 2 recovering 5.91 amp-hours and Sample No. 3 5.92 amp-hours of a new battery pack (new ≈6.0 amp-hours).
What Do These Results Mean for You?
When an automotive business rebuilds and/or conditions an HEV battery, there is significant profit margin for them to enjoy, without compromising the quality of repair to the customer. Labor time for removing and replacing a Toyota Prius battery pack whether conditioning, rebuilding or using a new unit is identical. Therefore, the costs are identical and cancel when analyzing total cost. The total number of labor hours for a technician to condition a Generation II Toyota Prius battery pack in this study is ≤ 2 hours for each battery pack. The cost to remove and replace the failed battery modules from Sample No. 1 (donor battery pack), No. 2 and No. 3 battery pack modules was ≈1.5 hours. Therefore, there was a total of ≈3.5 labor hours expended for the battery pack rebuilding and conditioning processes.
Therefore, if an estimate is used for the total cost of a rebuilt battery, it would range from $2,400 to $2,900. The cost difference between a rebuilt/conditioned battery pack and a commercially rebuilt battery pack, using the $2,400 cost target, is $1,938.72. Because the donor battery pack modules can be utilized in many additional battery pack rebuilds, the total of $800 is not added into the rebuild/conditioning costs. However, since the individual module costs have been factored into the total rebuilt/conditioned battery pack costs, the donor battery pack costs are/have been comprehended into the total cost.
With a cost difference between rebuilt/conditioned vs. commercially rebuilt units of $1,938.72, the profit that a service business could enjoy is considerable. Many aftermarket service businesses that are conditioning or rebuilding and conditioning are enjoying ≥ 60 percent profit margin.
As a technician or owner of an automotive business contemplating entering the HEV diagnostic and repair segment, there is one additional thought to consider. If conditioning and rebuilding battery packs is not in your future but you plan on purchasing rebuilt units there is relevance to what you have read in this article. Before your purchase battery packs from a supplier, ask them a few questions prior to making the purchase. Some of these questions could be:
• Can you supply battery pack Power test data?
• Can you supply battery pack energy capacity data?
• How many amp-hours is the battery pack rated when compared to new?
• What equipment is used to rebuild or condition the battery pack?
• Where did your technicians receive their training to rebuilding or condition battery packs?
• What components are tested as part of the rebuild process?
Is a warranty important? Of course it is. A minimum of a one-year warranty should be the minimum for a rebuilt battery. One other area of caution — there are many HEV companies on the market “claiming” to supply remanufactured batteries. Armed with a few questions and reviewing their products, you may find out that their battery packs are not remanufactured, but rebuilt units. Be diligent in pressing your battery supplier for proof of a remanufactured unit by asking for their BOM to find out what components are replaced that place the unit at new or better than new condition.
Not only will the service business that conditions or rebuilds and conditions HEV battery pack realize an excellent profit margin but the customer also realizes the benefits. Since there is a significant cost difference between a commercially rebuilt battery pack and a rebuilt/conditioned unit, the customer would realize cost savings of 40 percent or more. This is a “no brainer” for any customer that wants to save costs on a repair and receive a quality product.
Subscribe to Motor Age and receive articles like this every month…absolutely free. Click here
About the Author
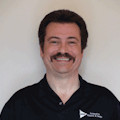
Mark Quarto
Contributing Editor
Dr. Mark Quarto is currently the Chief Technology Officer (CTO) for Automotive Research and Design, LLC. (www.go2hev.com). Key responsibilities include design/development of diagnostic test equipment and software, technical education and training programs, and technology innovations focused on Hybrid & Electric Vehicle Propulsion and Energy Management Systems. Dr. Quarto recently retired from General Motors Co. after 28 years with the last 16 years focused in Advanced Vehicle Development as an Engineering Group Manager for Advanced Powertrain Technology Systems / Global Aftermarket Engineering which included the development of control and diagnostics systems and service solutions for the Chevrolet Volt, Fuel Cell, Two-Mode Hybrid, Parallel Hybrid Truck (PHT), EV1 Electric Vehicle, S10 Electric Truck, and Alternative Fuel Systems Programs.