The story doesn’t always start with us. In fact, often, it does not. Maybe it’s our love for gathering and analyzing clues until we’ve solved the riddle or maybe, just maybe, we love pain. Regardless of the reason, when you get a reputation for solving problems that others want to set on fire, the fire comes to you. If you’re reading this article, I suspect that you have plenty of opportunities to play Sherlock Holmes with vehicles that others just want to make go away.
For today’s case, we have a 2017 Chevy Malibu with a 1.5L engine. The shop that first took a stab at the repair told us they had replaced the rack and pinion steering assembly andAfter our visual assessment, we realized that the power steering control module was part of the newly installed rack and pinion assembly, which was used. Not new or remanufactured. The fact that the power steering control module was serviced with the rack and pinion assembly wasn’t the problem per se, it was the fact that they were attempting to repair the vehicle with a used module on a vehicle that GM states should only be serviced using new modules. Starting in 2010 in the US, GM was transitioning their fleet to what’s called a Global A Architecture. This transition was complete by 2014, so our 2017 was definitely a Global A vehicle. What does that mean for you? Don’t swap modules on GM Global A vehicles — damage to both modules can occur.
I know what you’re thinking. “The 2010-2014 window is helpful, but how do I know which 2010-2013 GM vehicles are Global A?” During the transition, GM also changed the dealer scan tool from the former Tech 2 handheld scan tool used on non-Global A vehicles to the laptop-based GDS 2 (Global Diagnostics 2) scan tool for Global A vehicles. What’s really cool is GM makes determining which vehicles are supported by the Tech 2 versus the GDS 2 very easy by offering a couple handy charts (Figure 1, located for free on their website. Yes, I will provide a link.
Now that we have that out of the way, what are we going to do? You may consider trying to program the used module to this car since, according to GM, if there’s going to be a problem, the damage was most likely done when the used module was installed. All I can say is we didn’t have time for the mess if it got messy so we told the original shop to install a new rack and pinion assembly and we would program the power steering control module after they did so. The shop replaced the rack and pinion assembly, performed another wheel alignment and returned the vehicle to us to program and setup the replacement power steering control module. One of our technicians, Carlos Mercado, tried to get this vehicle completed before I returned from vacation, but no good deep goes unpunished. Carlos was a veteran technician when he began working with us, but in the four years he’s been on our team, his problem-solving abilities have grown substantially. As well rounded as Carlos has become, he hasn’t had a lot of opportunities to get acclimated with module programming because I perform most of our module programming off site for other repair shops. This is why I wasn’t surprised when I received a message from Carlos asking for the necessary login information to program the module. Throughout the text conversation, it was clear that there were complications, but being hundreds of miles away on vacation, I didn’t have the time to delve in. Fortunately for me, we have awesome friends. Tomi Oliva used a remote desktop software tool to take over Carlos’ computer and walk through the programming process to see what may be going wrong. He thought the rack and pinion assembly might be equipped with a power steering control module that may have compatibility issues.
When I returned from vacation, I visually inspected the rack and pinion assembly. It did look like a new genuine GM part, but I verified this with the original shop who did the install.
I connected a battery maintainer to the vehicle because a stable power source is needed for trouble-free module programming. I connected one end of our J2534 passthrough device made by Drew Technologies to the vehicle’s Data Link Connector and the other end to our Dell E7470 programming laptop, logged into our ACDelco TDS (Technical Delivery System) account and launched SPS, GM’s programming application. From there, we started the process of programming the power steering control module and the module programmed successfully with no problems (Figure 2).
When it comes to programming replacement modules on any vehicle, there’s usually some setup that’s needed after the module is programmed. With GM, module programming is not carried out with their dealer scan tools like some other vehicle manufactures. Instead, module programming is carried out using SPS (Service Programming System), GM’s module programming application. This means that if you don’t have a separate scan tool that’s capable of performing the setup or calibrations after programming the module, then you might be in trouble. GM has added some of these functions to SPS for late-model GMs. If you are new to programming, and something does not go as planned during the session, it may be difficult to identify the difference between a failure during programming or a failure during any functions performed after programming is complete.
On our Malibu, after the PSCM was programmed, some calibration functions needed to be completed. The replacement PSCM needed to learn the steering stop limits and the characteristics of the steering torque sensor and rotational motor. This is why Carlos thoughtAt this point, Carlos and I were on the same page. We recognized that the error occurred during the calibration and setup and not during the programming. This means that this function may be available in other scan tools so we tried several, including the dealer scan tool to no avail. We also noticed that when we were monitoring live data retrieved from the power steering control module using our scan tool, the steering torque sensor would respond when turning the steering wheel, but the steering angle sensor did not. It stayed at 0 regardless of steering effort or steering wheel position (Figure 6).
Was this a problem with the steering angle sensor or was it a product of an incomplete PSCM calibration? We dug into to our service information systems and couldn’t find the answer. Even researching our one and only C0460-4B Steering Wheel Angle Sensor Calibration Not Learned code retrieved from the PSCM didn’t give us much direction. We did, however, find that this vehicle does not have a steering angle sensor. This power steering system doesn’t use one. The PSCM compares motor rotation data with data received from the steering torque sensor and calculates steering angle (Figure 7).
We were starting to think that the lack of change in steering angle data was probably due to an incomplete setup, but we didn’t know how to prove that. So we got familiar with system and the circuits needed for this system to operate. It didn’t take long; the PSCM circuits are quite simple (Figure 8).
The PSCM had a single power feed, a single ground and a handful of bus communication circuits. We verified that the power and ground circuits were good. We did not expect that the communication circuits would be a factor, but it was easy enough to measure the CAN network circuits using an oscilloscope and the circuit voltages and activity was perfect.
We then asked the shop (our client) why the original rack and pinion assembly was replaced in the first place. Their answer was interesting — it was replaced due to a warning message in the instrument cluster stating that the power steering system needed to be serviced and a fault code that suggested the steering angle sensor was bad. We asked them to bring in the original rack and pinion assembly. We wanted to connect the original to the vehicle to see if there would be steering angle data displayed on the scan tool or what codes may set, if any. When they arrived, we removed the PSCM from the rack and pinion, which included the motor and all the related sensors. We then connected it to the vehicle harness and monitored the steering angle sensor data while we moved the steering input back and forth. The steering angle data just stayed at 0 regardless of the steering wheel position while the torque sensor data did respond to the changes in steering wheel movement.
With the original PSCM connected to the vehicle, we retrieved a steering angle sensor code, but it wasn’t the same code. I did not document the code number, but the description suggested that it was an internal fault. Our client decided to take the vehicle to the dealer service department and allow them to carry out their own diagnosis. They decided that the rack and pinion assembly was defective, so our client replaced the unit again, performed a wheel alignment and sent the vehicle to us. We again attempted to complete the programming and setup and found that the steering angle setup failed.
We needed the bay, so we pulled the vehicle out of the bay to make room for another, better paying one. When we backed the vehicle out, while turning the wheel very sharply, we noticed a rubbing sound. After some inspection, we determined that the right front wheel and tire assembly was rubbing against the lower control arm when the steering wheel was turned all the way to the right. The left front wheel was not. There were also more turns in one direction from a "centered" position than the other. This indicates that either the vehicle has damaged steering and/or suspension components or the rack andpinion was not centered properly during install or both. While inspecting the steering and suspension, we noticed that the left front strut had a camber kit installed. This would generally not be needed on a vehicle this new. This could indicate past impact damage, but no other obvious signs were found. We then inspected the steering shaftWe locked the steering wheel into a centered position, we then removed the steering shaft from the rack and pinion, made sure that the rack and pinion was in a centered position by turning the rack and pinion all the way to the left, then counting the turns as we turned it all the way to the right and then turning the rack and pinion back to the left half of the turns needed to go from full left to full right. Next, we reinstalled and secured the steering shaft using the correct size bolt then we performed a wheel alignment. Once we were finished, we reattempted the PSCM setup but this time, the setup procedure was successful.
In hindsight, the PSCM didn’t like the amount of steering wheel turns from stop to stop so it wouldn’t allow the calibration to complete. The rack and pinion was not properly centered and the tie rods were adjusted heavily to center the wheel. All of our troubles were caused by multiple poor rack and pinion installs.
About the Author
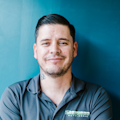
Brin Kline
Owner of Assured Auto Works
Brin Kline is the owner of Assured Auto Works in Melbourne, Florida, an automotive general repair business with a mobile diagnostic and module programming division. He has been in the automotive industry for 27 years. Kline also teaches for Carquest Technical Institute and Trained by Techs, is a member of the Automotive Service Association’s Mechanical Operations Committee, and president of the Automotive Service Association (ASA) of Florida.
Kline also reviews a variety of tools for Professional Tool & Equipment News. To read his tool reviews, search his name on VehicleServicePros.com.