3 problems with automotive inventory management
As humans, we can only keep so many pieces of information in our head. Fortunately, the technology in today's society helps us keep everything in order, if the technology is used correctly. Automotive inventory management tops the list of areas where technical support is needed.
High-powered auto repair inventory management software keeps track of fulfillment status and price markups for you, saving you time, stress, and mistakes. With less of a chance for error, the technology allows for a better customer experience.
For years, shops have tried to find the right balance between getting the parts your techs need – when they need them. However, it’s tricky to keep stocked without spending too much on parts that you’ll take years to use. How can you predict how many makes of each car will come into your auto repair shop?
Here are three hassles with automotive inventory management, and how to wisely keep pace with today's ever-growing world.
1. Sidestep stock shortages
Running short on auto parts makes it more difficult for your techs to stay productive. Even worse, it can lead to conflict with service advisors who have to report delays to customers. Meanwhile, advisors and parts managers track stock-keeping units with your automotive inventory management software based on turnover, age, and versatility. Ideally, they will use automated inventory control to reorder parts before they run out.
While many automotive parts departments do physical inventory counts annually, times have changed. Instead, reconciling stock more frequently via cloud-based automotive inventory management software can help ensure accurate inventory. In the long run, it reduces the odds of running out of the parts you need most.
With Shop-Ware’s auto repair inventory management software, for example, shops can automatically track parts on repair orders within one of three states:
- Not on premises, not on the way
- On the way
- On premises
Next, stocked parts that are kept in inventory get sorted into one of three states:
- Below stock, not on the way
- On the way
- Stocked at proper level
This tracking happens for every part on every repair order. Each state is color-coded in the UI and easily batched to take action.
2. Train your staff to succeed
Shops could just show a new employee a shop management system and expect them to learn the software alone. However, investing in training early pays off with more accurate orders and less stress for everyone. While auto inventory management can seem simple, organizing, forecasting, and keeping track of your parts requires many skills and expertise. For example, some auto repair software requires users to type in the exact name of a part to get a match.
Some shops go as far as hiring parts managers and workers that specialize in certain makes and models. Yet, most shops count on a smaller team to run their shop management software. Either way, investing time in onboarding your team to your auto repair software pays off in the long run.
View stocked parts and inventory control:
- Scan across your inventory to see what’s missing
- Order directly by vendor
- Organize your inventory by location
- Perform audits at any time
- Analyze stocking quantities based on recent turnover
- Look at purchase history for any part
- Follow numbers back to every single repair order for warranty or quality control issue
Just as with individual parts, your cores are a quick search away and returning and tracking returns is simple.
Create and track cores for all your parts
- Do this automatically when you order from an e-commerce partner
- View and track your cores and core returns
- Create return orders and track their status
- Complete all these tasks without printing any paper or managing files
3. Track automotive inventory management better
When you have large inventories, poor storage can lead to a wide range of problems. Just tracking and storing where parts are located can throw a wrench in your overall profitability.
Setting up proper processes and ensuring everyone follows them gets you off to a great start for a well-managed inventory. For starters, placing the most commonly used parts in the most accessible areas will save you time and headaches later. In addition, laying out your storage, so the parts are organized and placed in the most productive way helps as well.
Choose an auto repair software software that allows you to see the parts order status on each repair order. With Shop-Ware, for example, parts status' update live in real time, as changes occur on each repair order. Staff can visualize the part status across all repair orders in the shop or within your assigned group, allowing staff to respond promptly when needed. The technology allows staff to know when to dispatch jobs as ‘ready to start,’ which need parts, and which need immediate attention.
About the Author
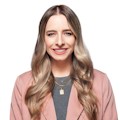
Laura Bussis
Laura Bussis is the product marketing manager for Shop-Ware, the leading shop management system. It offers game-changing features, such as DVX (Digital Vehicle Experience), Parts GP Optimizer, Advanced Analytics and Capacity. Learn more at GetShopWare.com or follow them on Facebook @GetShopWare, on Twitter @GetShopWare, on LinkedIn @Shop-Ware or Instagram @getshopware.