Tesla service, repair, and diagnostics
Although you may already provide service on Teslas, this article could reveal information you may not be completely aware of. Since Teslas fall into the “Software Defined Vehicle” (SDV) category, changes are continuously added to not only enhance the driver experience, correct for bugs and other issues, but are also rolling out changes to enhance the service technician’s experience as well. I now own two Tesla vehicles and over the past five-plus years I have witnessed many interesting changes that have allowed for better diagnostics and a way for those interested in learning more about how these machines work to learn more through the highly informational graphics displayed on the center screen when in service mode, and the theory of operation data now made available within service information via subscription. A quick example of this is shown in Figure 1 displaying the live thermodynamic heat-pump data values on a Tesla Model Y.
In this article, you will find plenty of graphics, explanations, and several use cases that I believe you will find to be highly informative. We will also cover how one can now access the vehicle remotely to triage and analyze vehicle problems before the vehicle arrives for service. I will also share an interesting case study where I was able to support a colleague, with a shop in Central California, in addressing a high-voltage battery problem on a 12-year-old Model S.
The role of automotive service technicians is evolving. With the advanced tools built into vehicles, such as those found on Teslas, you can experience the vehicles of the future today. The aftermarket service of Tesla vehicles poses unique challenges and opportunities, requiring a specialized understanding of Tesla's proprietary systems such as Toolbox, Garage, Periscope, and service information. This article aims to provide professional automotive service technicians with a detailed overview of Tesla Service, highlighting recent access developments and how they can leverage Tesla’s service tools.
Service Mode & Service Mode Plus
Going back about four to five years ago the aftermarket had no access to service mode or service mode plus unless you were a certified collision center. Today anyone can engage service mode through a couple of key presses on the screen. When accessing the software page and long pressing on the model's name of the vehicle for approximately five seconds, a password entry box should appear, and entering the word service will allow you to engage in service mode. A disclaimer screen will appear letting you know that you could get yourself in trouble if you don't know what you are doing. So, you should be cautious until you are highly fluent with Tesla vehicles.
On this first page (Figure 2), the first thing that I recommend doing is looking at the service alerts. This provides a list of alerts and warnings that may be useful when addressing vehicle problems or complaints. But beware, researching this information should be carried out before engaging in any level of diagnostics because I have seen several alerts and warnings for items that are known issues and that may be corrected sometime down the road through software updates.
Tesla Toolbox 3.0 Software
High voltage battery page
Tesla Garage
Sandbox
Maintenance services
- Alignment and tires – Tires for EVs have more demand due to vehicle weight and torque. Tires should be rotated every 5-6,000 miles. Wheel alignment checks can be done via software within service mode, but I have found many of these vehicles leaving the factory with wheel alignments that are not set up for optimum tire life. HVAC – The A/C system is an integral part of the EV systems and on pretty much all EVs. Therefore there are maintenance and inspections that should be performed on Tesla’s. Every five years Tesla states that the desiccant bag shall be replaced (Figure 9)
which of course will require an evacuation and recharge of the system.
- Brake Systems – The brakes rarely get used on an EV that is driven in a manner that is most efficient, but the braking system still must be able to stop the vehicle. Periodic inspections of the brake pads and rotors should be performed. Additionally, periodic maintenance on the brake caliper sliders along with brake fluid replacement should be performed as well. Check service information for more info.
- General inspections – Teslas use a lot of aero close-out panels which should be removed periodically for proper inspections. Looking for any anomalies such as hose or harness routing, evidence of critter exploration, drivetrain mounts, and heat exchanger airflow problems that can occur from the accumulation of debris between the condenser and radiators. Additionally, since BEVs weigh 20-30 percent more than their ICE counterparts, suspension wear and tear will likely present many service opportunities.
Case study – Model S battery issue
- Voltage: 385.3 V
- Battery Min Temp: 27 °C
- Max Temp: 28 °C
- Min Brick V: 4 V
- Max Brick V: 4 V
- SOC Min Unscaled: 81.8 percent
- Max Unscaled: 86.2 percent
- CAC Min: 239 Ah
- CAC Max: 239 Ah
- CAC Average: 239 Ah
Case study – Model 3 – Inertial measurement unit
About the Author
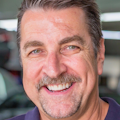
Scott Brown
Founder - Diagnostic Network
Scott is an ASE Master Certified Automobile Technician with L1, L3, & L4 credentials and has over 39 years of professional service industry experience. As an independent shop owner in Southern California and with his engagement at various levels of within our industry, he continuously strives to move the industry forward through networking, education, communications, and training. Scott is a founder of the Diagnostic Network (https://diag.net/) which was born in 2018 after he retired after 22 years at iATN, where he served as company president.
Brown is also the host of Professional Tool and Equipment News (PTEN) and VehicleServicePros.com podcast, Torque Factor. The podcast addresses the latest automotive service technologies while focusing on expanding knowledge and awareness around tools, equipment, education, and industry trends.